Residential Concrete Foundations – Prescriptive
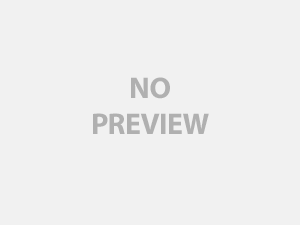
- Prescriptive Foundations – General
- Conventional Light Frame (Wood) Construction
- Prescriptive Construction Bracing
- Anchor Bolts and Tie Downs.
- Soil Type
- Frost Depth
- Foundation Wall and Footing Size
- Foundation Details
1. General
The purpose of this lesson is to enable (embolden) you (the Architect, or `Designer’) to design prescriptive foundations (yourself) and thus not require the services of a structural engineer (me). Fees come with our services. And if there are designs that you can do without us, why not?
Prescriptive design is basically `following the rules’ (prescription). If you stay within the `limits’ of the prescriptive code, it (the code) will provide you with solutions.
The most common example of prescriptive foundation design is that for Residential construction. In general, if the superstructure construction falls within certain limits of the code, then there are prescriptive provisions in the code for the foundation. An example of such is prescriptive foundation for conventional light-frame wood construction.
Where light frame conventional wood construction is less common for residential construction, local building codes may provide prescriptive foundation design for other common construction types.
If part, or all, of the proposed construction does not fall within the limitations of the prescriptive code, then such parts, or all, of the foundation may need to be engineered
Note: both the International Residential Code (IRC) and International Building Code (IBC) have prescriptive foundation design provisions. The local building authority will generally adopt one, or both of these, with amendments, modifications, etc., for use in residential construction in its jurisdiction.
2. Conventional Light Frame (Wood) Construction
Reference: IBC 2308
Table 1805.4.2 of the International building Code provides minimum footing widths and thicknesses and other construction details for conventional light frame construction as a function of floors supported.
The term conventional light frame wood construction as used in the code is not meant to be taken as `all stick frame construction’, but light frame wood construction within certain boundaries. These limitations are found in Chapter 23 of the IBC and are summarized below.
Limitations of Conventional Light Frame (Wood) Construction
- Three stories above grade.
- Floor to floor heights not exceeding 10 ft.
- Loads not exceeding
average dead loads of roofs, floors, and walls not exceeding 15 psf
40 psf floor Live loads
ground Snow loads not exceeding 50 psf
- Basic wind speed (3-sec gust) not exceeding 100 mph for Exposure Condition C and 110 mph in Exposure Conditions A,B.
- Roof trusses or rafters spanning not more than 40 ft
- and so on.
It is prudent that you as the Architect are familiar with the above in the initial design stages with your Owners. In cases where the Owners are desirous of construction that falls outside these limitations (more stories, heavier construction materials, etc.) you can advise them early in the process that additional design fees will be necessary as the foundation will thus have to be `engineered’.
3. Prescriptive Construction Bracing
Reference: IBC 2308.3
Before we move into the details of prescriptive foundation design it is also important to look at bracing requirements for prescriptive above ground construction.
In general, continuous foundations will be required at bearing walls and brace wall lines.
As much as I would like to, I will not get into superstructure bracing in depth. However, the prescriptive code for the superstructure provides bracing requirements that affect our foundations, so I will cover at least a little, here.
Basically the codes require that our structure be braced against the action of wind or seismic ground shaking. Bracing in normally accomplished in light frame wood construction using braced wall panels. These panels are constructed in a number of different ways but basically involve a certain minimum length of wall be sheathed from floor to ceiling with some kind of structural panel or sheathing. A typical braced wall panel made of wood structural panel sheathing must have a minimum length of 48 in. These panels are placed on braced wall lines. The code specifies how often along these lines we must have such panels, and how far apart the braced wall lines may be spaced (from each other).
One example of such requirements is that the braced wall panels be at (or near) the ends of each wall, may not be farther apart than 25 ft o.c. on any braced wall line, and the maximum distance between braced wall lines is 35 ft. The code goes on to require that braced wall lines must be supported by continuous foundation. Hence, our foundation design must accommodate the braced wall lines needed for bracing (requiring interior foundations where we might otherwise not have planned for them).
Note: the IRC appears to be less demanding on the issue of continuous foundations for interior braced wall lines, especially in areas of lower seismic risk.
The details of the code will also specify the anchor bolt and tie-down requirements of braced wall panels. Traditionally the anchor bolts and the embedded portion of the tie-down hardware is cast-in-place during the construction of the foundation. However, post-pour anchor and tie-down devices are now available that relieve the foundation contractor of placing the anchors and tie downs in the foundation as it is being cast.
Note: while bracing and other requirements of the `codes’ across the country have a lot in common (and often derive from the same model code(s), e.g., the IBC and IRC) there are differences. And, not only are there differences in the code(s) jurisdiction to jurisdiction, codes change (in time). So, you must familiarize yourself with the codes in force in the jurisdiction of your project at the time you are applying for your building permits. (Don’t just take my word for it. You and I may even be in the same jurisdiction, but by the time you read this, the code has changed.)
So, now, summarizing, we need `foundation’ at:
- Exterior walls
- Bearing walls
- Braced wall lines
4. Anchorage and Tie-Downs
Anchor bolts are generally required to `anchor’ the wood framing of the superstructure to the concrete elements of the foundation. Wood in contact with concrete is generally required to be preservative treated (against decay), as concrete tends to wick soil moisture. There may be exceptions to the preservative treatment requirement where it can be demonstrated that moisture is not a consideration. Generally the framing is attached via a sill plate. These are typically 2 in. nominal in thickness, though some jurisdictions, such as those with greater seismic risk, may require 3 in. nominal plates.
While anchor bolts are intended to resists the superstructure `sliding’ off the foundation, tie-downs may also be required to `tie elements down’ in resistance to uplift / vertical forces. In prescriptive construction tie-downs are typically required at the ends of `Alternate Braced Wall Panels’ or their manufactured equivalents, where the `racking’ action on each panel tends to pull up the panel ends. These tie-downs are additional to anchor bolt requirements.
An example anchor bolt requirement (but somewhat typical) follows:
… Ã?½ in. diameter bolts @ 6 ft o.c. sill to foundation
… cast-in-place anchor bolts are generally required to be embedded 6 in. or 7 in.
In areas of greater seismic risk 5/8 in. diameter bolts may be required, and/or washers of min. specified dimensions.
Post-cast anchors of shorter depth will probably be allowed if they can be demonstrated to provide the equivalent lateral resistance as the cast-in-place anchors.
Note: in addition to the general requirement of bolts @ 6 ft o.c., or whatever, the code also generally specifies placement of bolts in each piece of the sill plate (not less than 2 bolts per piece, and bolts at the ends not less than 4 in. and not more than 12 in. from each end … IBC 2308.6). One advantage to the post-pour anchors is that the foundation contractor doesn’t have to guess (or dictate) where ends of individual sill plate pieces will be (since many foundation walls are quite longer than the sill plate pieces available at the lumber yard).
Cast-in-place anchor bolts are generally L-shaped or J-shaped, or may be cast in place with the bolt head down. Anchors with the head cast down have the greatest resistance to pull-out. However, as mentioned above, generally anchor bolts are intended to resist lateral (sliding) action, not pullout (uplift). If an anchor is to be used (also) to resist uplift forces, the head-down arrangement should be used or some other arrangement or hardware that has been tested in that capacity.
Tie-down anchors may be embedded bolts or manufactured hardware for that purpose. Generally the code will specify tie-down hardware be used meeting some minimum uplift load. Manufactured hardware can then be selected that meets or exceeds the code requirement. Obviously the hardware must be installed per the manufacturer’s recommendations and requirements to meet the rated loads.
5. Soil Type
Our Rx foundation will generally depend on the type of soil we are founding our building on. Or not. The reason I say `or not’ is that earlier editions of the model codes provided footing width and thickness values irrespective of the type of soil being founded on. And many local jurisdictions followed this approach, and perhaps still do. In this section, however, we will look at prescriptive design of a footing using the 2006 IRC, which does take into account soil type.
Before we get started, one `type’ of soil you should NEVER build on, is `fill’. By this I mean `uncontrolled’ fill. Soil that has been moved around by anything other than `nature’. `Controlled’ fill in this context means fill that has been placed in a controlled manner, AND, for which, an engineer is willing to, and HAS certified that it meets certain specifications (or will certify that it does).
Sadly, many a good structure has been ruined by being founded on poor soil (uncontrolled fill).
So (or but) assuming that we are embarking on a project without the services of a soils engineer, the code provides us with a way to design our footings/foundation based on the type of soil we are founding the building on, providing the soil is undisturbed / in its natural state.
First we need to determine the type of soil the structure will be built on. Some ways to do this are:
- U-Dig … simply go to the site with a shovel and start digging, and then `look at’ the soil,
- U-Have-Someone-Dig … contract with someone else to dig (especially if you have to go deep), and `look at’ it,
- Soil Survey … see if the location of your site has been `surveyed’ by others. For example, the Natural Resource Conservation Service (NRCS), formerly the Soil conservation Service (SCS), has surveyed the soils of much if not all of the lands with agricultural potential and provides soil profile information and general suitability for various uses, including suitability for structures.
- Ask Around … see what information the site owner, building official, and/or local contractors have on the soils in question.
- $oils Investiga$ion … contract with a soils / geotechnical engineering firm, as already mentioned; however, the topic of this particular section is obtaining information possibly without having to hire one.
For some projects it may be sufficient to to simply do some digging, `look at’ the soil, and be able to generally classify the soil and identify other site conditions that need to be known (slope, surface and ground moisture conditions, etc.). As the Architect for the project there will be a good chance you will be visiting the site anyway, so, on one of those visits, `look at’ the soil.
Soil/ground type and conditions may also be obtained by `asking around’. A lot of information can be obtained this way, but it is not always good information. Remember that as the Architect you are the one who is supposed to know, and you are the one who will be in trouble if something goes wrong. So, use the information provided by others, particularly if they have not `stake’ in the project, with discretion.
Also note: while the building official may be able to provide useful information with regard to the soils of your site, he / she is not, nor will be, responsible for this information. Quality control, including that of the soil, is ultimately the responsibility of the Owner.
Further note: in some areas the soil is so `bad’ (or potentially bad) for construction that the local building authority will require soils investigations for ALL construction projects, even residential construction projects.
Unified Soil Classification System
With regard to construction, soils are often classified according to the Unified Soil Classification System.
Here … http://en.wikipedia.org/wiki/Unified_Soil_Classification_System
Allowable Bearing Pressure of Soil
Once the Soil Type is determined, the presumed allowable bearing pressure of the soil may be obtained, for example, using IRC Table TABLE R401.4.1.
So, let’s say you go to the site of a proposed residence, you dig down through the pine needles, other forest litter, etc., and find sand. Silty sand. You dig deeper and find more (silty) sand. You did as deep as the footings are anticipated to go, and still (silty) sand. And it appears that the site is essentially undisturbed.
According to the Unified Soil Classification System, silty sand is denoted SM.
Table R401.4.1 gives us an allowable soil bearing pressure of 2000 psf for silty sand (SM).
6. Frost Depth
Before we design the foundation wall and footing we need one more important piece of information. And that is the `frost depth’ – more particularly the maximum anticipated penetration of freezing temperatures into the soil profile. Footings must be placed below this depth (at least the bottoms of the footings). The reason for this is to avoid `frost heave’ – expansion and contraction of soil as it freezes and thaws. The differential movements of soils as they freeze and thaw can `break’ even the best-designed footing.
The general practice of construction is to place the bottoms of footings below the frost depth. There are exceptions, however. By specifying a certain penetration into the soil, the soil adjacent to the foundation is assumed to provide `insulation’ against freezing. If an alternative way to prevent freezing temperatures at the footing depth can be demonstrated, it may be possible to use shallower footings. Some jurisdictions accept some such systems, called Frost-Protected-Shallow-Foundation systems (FPSF).
Generally the frost depth for any location is provided by the local building authority. Obviously in warm climates the depth is shallow or non-existent. In my locale it is 30 in. In colder areas the depth is even greater. But not always. Some jurisdictions count on heavy snow cover as providing insulation to foundations, and as such, may have relatively shallow prescribed frost depths. As a designer I view shallow frost depths in snow areas with some caution as I consider possibilities of snow (insulation) removal by wind, snow removal practices, etc.)
7. Foundation Wall and Footing Size (Design)
We’re now essentially ready to do our first simple `design’.
Let’s consider an exterior wall foundation for a structure that will be supporting a main floor, an upper floor, and a roof. The soil is silty clay, and the local frost depth is 30 in. And the roof Snow load is 40 psf. Construction will be conventional light frame (wood) construction (as defined in the `code’).
In the most simple sense, the design will include:
- Foundation wall thickness
- Foundation wall height
- Foundation wall reinforcement (vertical and horizontal)
- Footing width
- Footing thickness
- Footing Reinforcement
- Exterior Finish Grade level (accommodating frost depth)
So, let’s do it.
1. Foundation Wall Thickness.
The IRC minimum is 6 in. Local jurisdictions may prescribe otherwise. In this area I find 8 in. to be the practiced minimum. So, for this example …
… foundation wall thicknesses … 8 in.
2. Foundation Wall Height.
The models codes will require some minimum distance between finish grade (earth) and wood (wood not protected by preservative treatment or otherwise resistant to moisture effects) … typically 6 in. or 8 in.
Assuming ahead of time that our footing thickness will be 8 in., and that we will require a minimum distance of 8 in. between finish grade (F.G.) and the wood portion of our superstructure, the minimum wall height can be calculated from the required frost depth protection …
Frost Depth + 8 in. clear to wood = wall height + footing thickness …
So, for a frost depth of 30 in., clearance of 8 in., and anticipated footing thickness of 8 in., we get …
wall height = 30 + 8 – 8 = …
… 30 in.
3. Foundation wall reinforcement …
IRC … horizontal … one # 4 bar within 12 in. of the top of the wall and one # 4 between 3 in. and 4 in. from the bottom. (For taller walls more horizontal reinforcement may be required.)
Horizontal reinforcement causes the foundation wall (called a `stemwall’ where relatively short) to act like a reinforced concrete beam at grade.
Vertical reinforcement requirements vary widely jurisdiction to jurisdiction. The IRC and UBC require reinforcement on the basis of wall height and the amount of soil being retained (difference between soil heights inside and outside the wall). The IRC does not require any reinforcement for some cases of short wall heights. HOWEVER, local jurisdictions often do, and will generally amend such information into their local codes.
For this jurisdiction vertical bars are required at not more than 48 in. o.c.; additionally, horizontal bars may be spaced not more than 24 in. o.c.; thus, for a 30 in. wall, following the other placement requirements, at least three bars will be required.
So,
Horizontal Steel Reinforcement (H.S.): # 4 @ 24 in. o.c. with the top bar within the top 12 in. of the wall and the bottom bar between 3 in. and 4 in. from the bottom.
Vertical Steel Reinforcement (V.S.): # 4 @ 48 in. o.c., embedded 6 in. min. into footing.
4. Footing Width. Minimum widths are generally provided by table and are a function of number of floors (and roof) supported and soil (allowable bearing pressure). Using IRC Table R 403.1 for a structure on soil with an allowable bearing pressure of 2000 psf (the silty sand of example), light frame construction, we get a min. footing width of 12 in.
Note: actually, around here, we have almost entirely clay and silty clay soils for bearing, which will result in a minimum width, from the Table, of 15 in.; and the local code, deriving from the IRC, simply uses 16 in. for all soil types.
So, for the sake of our example … width = 12 in.
5. Footing Thickness. Minimum thickness values are either prescribed by table or by formula. The IRC requires that the footing thickness be such that the projection (P) of the footing from the face of the stemwall be not greater than the depth of the footing. In the case of our example, the wall width is 8 in.; the footing width is 12 in.; so the projection on either side will be …
P = (footing width – wall width) / 2 = (12 – 8) / 2 = 2 in.
This is a ridiculously thin footing. Alas, the IRC also says that the minimum thickness is 6 in., and local jurisdictions may require 8.
For the sake of our example … thickness = 6 in.
6. Footing Reinforcement. For relatively small footings generally reinforcement is required only in the `longitudinal’ direction (parallel to the wall). A typical requirement is 2 – # 4 bars. For wider footings carrying greater loads `lateral’ or `transverse’ reinforcement may be required. For the smaller, relatively lightly loaded footings, however, as long as the footing is `thick enough’, we will find that it is also `strong enough’ without the lateral reinforcement. (We’ll demonstrate this in calculations later in the course.)
So … footing reinforcement: 2 – # 4 longitudinal.
Finally,
7. Finish Grade and Frost Depth. We’ll simple draw and note that the footing must be placed at least 30 in. below grade, and indicate the 8 in. clearance between F.G. the top of the foundation.
A stemwall of the height in this example will also generally accommodate crawl space clearance requirements, which we will address in greater detail later.
So, … footing shall be placed min. 30 in. below finish grade and finish grade shall be at least 8 in. below wood superstructure.
Note that if the site is sloped along the direction of the foundation, the stem wall height may vary, and need to be `stepped’ to accommodate the above.
NOTE: the above example is for an exterior wall foundation (wall and footing).
Interior foundation requirements follow a similar `path’ with some exceptions such as … frost depth is generally not an issue. If the interior main level or basement floor is to be a concrete slab, often such footings are cast monolithic with the slab (thickened slab). If the bottom floor is wood framed, often a short framed wall across the crawl space is used instead of a concrete stemwall.
8. Foundation Details
There are a lot of other details to cover in the design of our foundation; however, we will wait until we have done some `calculated’ foundation sizes before we cover them.
Calculated Footing Sizes … here.
Foundation Details (Features) by Calculation … here.
Details … here.
9. References
International Building Code, International Code Council, 4051 West Flossmoor Road, Country Club Hills, IL 60478.
International Residential Code, International Code Council, 4051 West Flossmoor Road, Country Club Hills, IL 60478.