Cutting and Installing Crown Molding the Easy Way
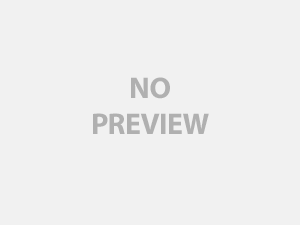
The problems begin when it is discovered that for some strange reason, 45 plus 45 doesn’t equal 90 when making a standard miter cut on crown molding. Actually, the reason isn’t really all that strange, but there’s no need to get into the details. The main concern is finding the angles that work.
If you’ve had that unpleasant experience, and have sworn off crown molding ever since, here are the tips you have been looking for. You’ll be able to cut and install crown molding like an expert in no time, with much less effort than you think. And best of all, there will be no wasted material and trips back to the store.
The following settings and procedures are intended for walls and ceilings with 90-degree corners, using the most commonly available types of crown molding. Projects that involve cathedral ceilings and other angled surfaces are much more involved, and should be handled by experienced crown molding installers. Working with the simplest projects first is by far the best way to gain experience. And once you have that, you can start thinking about the more complex jobs.
First of all, a conventional miter box just isn’t going to work for crown molding installation. You’re going to need something a little more sophisticated. The ideal tool is a compound power miter saw. It will perform all the necessary functions and is portable enough to tote and set up anywhere.
In addition to the miter saw, you’ll need a hammer, 4d or 6d finishing nails, tape measure, nail set, fine sandpaper, and some wood filler or spackling. A drill with a very small bit is a good idea also.
It should be pointed out that the letter “d” in nail sizes stands for “penny,” so if a salesperson comes along to offer assistance, you’ll know what to ask for.
Let’s get back to our standard 90-degree surfaces. There are two methods of cutting crown molding to fit them. One is to position the molding on the miter saw’s fence and table at the same angle it will be when it’s installed against the wall and ceiling. In that case, the conventional 45-degree miters are the correct cuts. And that’s the way most instructions tell you to do it. However, that method can present a major problem. It may not work. If your miter saw doesn’t have a high enough fence to rest the molding against, especially when wide molding is used, you’d be out of luck. Plus, if you don’t position the piece perfectly, the cut will be wrong. Fortunately, there’s another way.
It’s much easier to cut the molding while it’s laying flat on the saw’s table and against the fence. The height of the fence and width of the molding aren’t an issue. But in order to do this, the miter will have to be set at an angle other than 45 degrees. The correct angle to set the miter is 31.6 degrees.
There’s another angle involved, and that is the bevel – the angle to set the blade. That is 33.9 degrees. Fortunately, all power miter saws have the angles clearly marked, and many of them already have these correct crown molding angles highlighted, so it’s a simple matter of setting them. The machine may even have a miter locking stop at 31.6, which makes it even easier.
Remember, these angles will only work for cuts made when the molding is placed flat on the saw’s table.
There are four basic miter cuts for crown molding. They are inside left (IL), inside right (IR), outside left, (OL), and outside right (OR). For all four of these cuts, the miter is set at 31.6 degrees, and the bevel is set at 33.9 degrees. The only changes you will make to the saw will be setting the miter left or right.
The molding piece must be positioned on the saw correctly; the top against the fence for some cuts, the bottom for others. And you will also have to be aware of which piece will be the finished one after the cut.
If this is starting to sound confusing, don’t despair. It really isn’t, and once you start with some sample cuts, it will become very clear. That’s where the next tip – a very important one – comes in.
Before jumping into the project, head out and pick up an 8-foot piece of the cheapest crown molding you can find. It should be at least 2Ã?½ inches wide. Once you have that, you’ll need to make four sample pieces of molding, each with one of the four basic cuts. Make standard 90-degree cuts at the opposite end of each piece to avoid confusion. Mark each piece according to the type of cut (OL, IL, OR, and IR), and which is the top surface.
The sample pieces don’t need to be any longer than a foot or so. That way you’ll have some extra material available if you make a mistake. And be sure to save the four pieces after you’ve cut them. They will become valuable reference tools when you’re cutting the actual molding, as you will soon discover.
Make sure the miter saw has been properly adjusted before making any cuts. The owner’s manual contains detailed information on making adjustments.
Following are the procedures for the four basic cuts. Remember, the bevel is always set at 33.9 degrees, and the finished side of the molding is always facing up. Refer to photos.
IL (inside left)
Miter setting 31.6 degrees RIGHT. Top of molding is placed against saw’s fence. The left piece will be the finished piece after the cut.
IR (inside right)
Miter setting 31.6 degrees LEFT. Bottom of molding is placed against saw’s fence. The left piece will be the finished piece after the cut.
OL (outside left)
Miter setting 31.6 degrees LEFT. Bottom of molding is placed against saw’s fence. The right piece will be the finished piece after the cut.
OR (outside right)
Miter setting 31.6 degrees RIGHT. Top of molding is placed against saw’s fence. The right piece will be the finished piece after the cut.
When you have made the four cuts and marked each piece, test them. The two pieces with the inside cuts placed together should create a perfect 90-degree corner, as should the two with the outside cuts.
If the pieces don’t result in 90-degree corners, there are three likely causes:
1) You positioned one or more pieces on the saw improperly, or used the wrong piece as the finished one. Refer to the instructions and make any necessary cuts again.
2) The saw may be set incorrectly. Make sure the miter and bevel are set at the proper angles, and securely tightened in their positions.
3) Debris may have been caught in between the molding and one of the saw’s surfaces. Make sure the saw’s work surfaces are clean.
Once you have pieces that create perfect corners, you’re ready to begin the project.
When you buy the actual crown molding, it’s always a good idea to pick up at least one or two extra pieces. Many projects have a tendency to run short on material.
Now it’s time to begin cutting the final pieces for the actual installation. This is where most of the confusion begins, since it’s not always that easy to determine which type of cut is required. One mistake can ruin an expensive piece. That’s where those four pieces you cut earlier will come in handy.
Why are these four pieces so important? Well, here’s a typical scenario. You examine the area, determine that an inside left cut is required, grab the expensive piece of crown molding, and place it on the saw. Now what? Are you sure it’s an inside left? Does the top or bottom go against the fence? Left or right miter?
Using the four sample pieces eliminates the confusion and guesswork. When planning a cut, find the sample piece that matches the cut that will be required. Holding it against the wall and ceiling in the actual location makes this easy to determine. The photo shows a situation that requires an inside left cut, which is clearly marked on the piece. The top of the piece is also noted.
Then place that piece on the miter saw and match the miter and bevel to the cut. You’ll know instantly whether the miter is left or right, whether the top or bottom of the molding rests against the fence, and which piece will be the finished one after the cut, so you can position the saw and the good piece of molding accurately. And at that point, you’re ready to make the actual cut.
Throughout your project, the only saw adjustment you will have to make will be to the miter, left or right. The bevel setting will not change.
Experienced installers obviously don’t need these four pieces, and can instantly determine which cut is required. Anyone who does it often enough will develop a knack for it, just like anything else. But for those of us who don’t install crown molding all that often, the pieces are vital tools that can save a lot of headaches, time, and money.
There’s another factor involved in crown molding work, and that is precise measuring and marking the pieces. Extreme accuracy is a must. Close enough is no good. As an added precaution, you might want to cut the piece slightly longer than you think it should be. If it’s too big, it’s easy to shave off a little. It may mean an extra trip or two to the saw, but that’s easier and cheaper than an extra trip to the store.
When installing the finished pieces, locate the wall studs beforehand. They’re normally spaced 16 inches apart, but you may encounter 24-inch spacing. Don’t drive the nails at 45-degree angles through the center of the molding. Nails should be driven straight in near the edges, where the molding fits flush against the wall and ceiling. Notice in the photo how the molding is positioned.
Drilling small pilot holes into the molding before nailing is recommended. This can prevent splitting it. Then drive the nails directly into the wall studs, but not all the way in at first. Leave enough sticking out so you can easily remove them if needed. An adjustment or two, especially at corners, is often required. Even after everything is in place and looks great, don’t drive the nails “home” as carpenters put it, or you could damage the molding with hammer blows. Use the nail set to sink the nails slightly below the surface. Fill in the holes with wood filler or spackling, and they’ll become nearly invisible.
If you miss a stud, it’s no cause for alarm. You can pull the nail out or simply leave it there to sink with the nail set later. You’ve already made the hole and it’s going to have to be filled in anyway. Using a stud finder and old-fashioned tapping on the wall are other methods of locating studs.
Ceiling joists are a bit different. Molding pieces running at right angles to the joists can be nailed into them without any problem. However, it’s not that simple on lengths of molding that run parallel with the joists. You won’t be able to nail into them unless you’re very lucky and the molding happens to be directly underneath one. But the chances of that are slim at best.
So what’s the solution? You can nail directly into the drywall, but that doesn’t provide much holding power. Fortunately, not much is needed as long as the bottom of the molding is securely fastened, so it usually works. Many pros install an angled backing board behind the molding to use as a nailing surface, but that starts to get quite involved. Using adhesive is another method, and that’s probably the best one. Just remember to wipe up the excess before it dries.
Longer walls will require two or more pieces of molding butted together. Don’t simply make a straight cut on the two pieces. The correct method is to make beveled cuts. The result will be a much smoother seam where the pieces are joined.
For example, the easiest cuts for butting two pieces together are the same ones you use on corners. You can make an IL cut on the left piece and an OR on the right one, and they will fit together in a straight line perfectly. Referring to your sample pieces can eliminate the guesswork here also.
Slight gaps in the finished joints and other areas may occur now and then, due to imperfections in the wall and/or ceiling. Most homes don’t have perfect 90-degree corners and flat surfaces, but for the most part it doesn’t present a big problem. It’s possible to adjust the miter to compensate for imperfect corners, but it should only be done as a last resort, and then very slightly. Overdoing it can make things worse. Unless they’re extreme, unsightly gaps can normally be filled in with wood filler or spackling.
If you absolutely must adjust the miter, make sure to return it back to 31.6 degrees before cutting the next piece.
Lightly sand the molding where needed, especially at seams, corners, and any locations where wood filler was added. Gather up your four sample pieces of molding and place them in a container so they’ll be ready for use on your next project.
Then it’s time to grab a little refreshment of your choice, stand back, admire your handiwork, and congratulate yourself on a job well done!