Is Your Condominium Becoming a Dangerous Place to Live
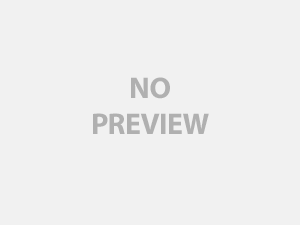
Structural concrete restoration consists of repairing deteriorated concrete and rusted reinforcing steel to bring the structure back to its original specifications and condition. Structural damage is often found on elevated slabs and catwalks, decks and parking areas. In Florida, most structural concrete damage is caused by moisture intrusion resulting in the rebar rusting.
When moisture penetrates the concrete it causes the rebar to rust. As rebar rusts it expands up to seven times its original thickness exerting a force of over 10,000 psi that causes large cracks and spalling concrete. Seemingly insignificant problems on a building’s surface may be outward indications of much more serious problems beneath that can only be determined by a qualified, experienced structural engineer
Basic Repair Methods:
- · Removal of existing concrete
- · Coating the steel rebar
- · Replacing the Concrete
- · Remove and replace expansion joints
- · Application of waterproofing membrane
- · Mechanically cleaning the steel rebar
- · Post-tension cable repair
- · Application of corrosion inhibitors
- · Rout and seal concrete cracks
- · Application of decorative coatings
Words and Abbreviations to Know
AIA
American Institute of Architects
AutoCAD
Program used to create the drawings of the balcony and show the repaired areas.
Bond
Payment and Performance Bond is acquired by the contractor (at the associations expense) to insure that the contract is completed and all sub contractors and suppliers are paid.
CF
Cubic Foot
CGC
Certified General Contractor
CO
Change Order
Design Mix
Special mix of concrete and corrosion inhibitors
Engineer/Threshold Inspector
Structural Engineer must also be qualified as a Threshold Inspector. This allows them to submit a Special Inspectors letter with the Permit Application. This means that the Engineer will act as the inspector and send inspection reports to the building department as the job progresses.
ICRI
International Concrete Repair Institute
LF
Linear Foot
MCI
Migrating Corrosion Inhibitor
MH
Man Hour
Overhead Spall
Spall located on the ceiling of a deck, patio, balcony or catwalk Structural
PSI
Per Square Inch
Rebar
Reinforcing steel located in a slab
SF
Square Foot
Slab spall
Surface spall located on a deck, patio, balcony or catwalk
Spall
Deteriorated concrete
Through Spall
Spall that goes completely through the deck, patio, balcony or catwalk
Regular Building Inspections
It is recommended that the association hire a Structural Engineer to perform an inspection of the building every few years. However, there are some signs of concrete deterioration that can be found by a simple visual inspection performed by maintenance personnel and managers. With the awareness and assistance of the manager, boards of directors may be alerted in the early stages that risk may be at hand. Some common risks are:
- Concrete spalling – the deterioration of concrete
- Lifting tile – tile that is raised due to deteriorated concrete
- Rust spots
If a restoration project is necessary, it would also be the time for the association to consider doing other related work such as; upgrading sliding glass doors and/or shutters, railing replacement, and painting of the entire building.
Understanding the Importance of the Work
A restoration project is a straightforward process. Difficulties can arise when there is a lack of a knowledgeable team, inadequate planning, incomplete information, poor communication, and poor worksite preparation. There are procedures that will help ensure proper repairs while minimizing unexpected problems.
The first step to a successful restoration project is communication, insuring the board of directors, manager, and owners understand the importance of the repairs. When there is doubt by the owners that the work is necessary to protect the integrity and safety of the building, the project will most likely experience interference by owners. This will resulted in increased cost and cause delays to the completion of the work.
Plan For The Funding Of The Project
The directors must consider their options for funding a concrete restoration project. Does the association have sufficient reserve funds for the project? Will the board need to special assess the owners? Will the board choose to borrow funds from a lending institution? These decisions take time and consideration. If special assessments are needed or if the association will be asking owners to move reserve funds from one account to another, the time needed to call such meetings and obtain the necessary votes should be taken into consideration. If a loan is deemed the best source of funding, the loan process can be long and not result in a loan for the full amounts needed.
Timetables
- Timetable – for selection of the Engineer, two to three weeks
- Timetable – for selection of the Contractor – six to eight weeks
- Timetable – for contract negotiations – two weeks
- Timetable – for acquiring permit – two weeks
- Timetable – for work to begin – five days after permit is issued
- Timetable – for completion of work – to be submitted with bid based on estimated quantities. As the project proceeds, the timetable should be revised monthly.
Selecting Your Restoration Team
Once it is agreed the concrete repairs are necessary, it is important to select the proper team for a successful concrete restoration project.
Association Representation – The team begins with at least one member of the board of directors, the manager, or other interested persons who will be responsible for administration, adequate funding and the day-to-day management for the project.
The Engineer – The next team member to select is a competent and experienced structural engineer that is also a threshold inspector. Selecting a structural engineer begins by interviewing several engineers in the area with a record of accomplishment for successful concrete restoration projects.
Since the building departments are not equipped or willing to perform the inspections required on a restoration project (because of the use of swing stages and mast climbers going very high – some buildings are 30 stories/300 feet), the Structural Engineer must also be qualified as a Threshold Inspector. This allows him to submit a Special Inspectors letter with the Permit Application. This allows the Engineer to act as the Inspector and send inspection reports to the building department as the job progresses. However, the building department still needs to be notified about the inspections and a copy of the inspection letter goes in the permit package posted at the job site so that a building department inspector can come by and check it. This is all handled by the Engineer and the Contactor.
Important Interview Questions:
History of the company
Who are the owners of the company?
How many inspectors vs. projects?
Concrete repair project history.
It is important that the engineer recognizes its responsibility to the association but also has a track record of dealing fairly and honestly with restoration contractors and has a staff adequate to provide timely inspections and meetings as required without causing delays. The engineers will also present of list of their fees before a contract is signed with them.
The engineer chosen will survey the building and provide an estimated budget for the work based on estimated quantities of repairs, this will enable the board of directors to determine what funds are available or need to be raised by assessments or a loan program. Then engineer will prepare and administer a bid package to solicit bids for the estimated scope of work to qualified contractors and assist the association in reviewing the bids. The engineer also provides signed and sealed specifications required for the permit, direct the contractor where to make the repairs and marks those areas, inspect the repairs as it is be done and after the repair is completed. The engineer also issues inspection letters and issues a final inspection letter to the building department stating that all work was completed as specified. The engineer reviews the contractors bills and approves them based on authorized repair quantities.
There is no known method of inspection that can “see” the full extent of the deterioration until the concrete is actually chipped open to expose the amount of deterioration of the reinforcing steel inside the concrete. Because the full extent and scope of the work cannot be known beforehand, yet must be completed to these rigid standards, the actual quantity of repairs often exceeds the estimates. This explains why concrete repair projects are bid on a fixed unit price with estimated quantities. Many engineers recommend that associations budget a contingency of about 25 percent. This ensures funds are available to complete repairs properly without having to go back to the owners or the bank for additional funds. In addition, since the contractor will bill only for actual quantities of repairs completed, if work turns out to be less than estimated, the excess funds can be returned to owners or saved for future repairs. For this reason, hire an independent engineer rather than one who works for the contractor. Most engineers approve payments only for work they expressly required and approve. Change orders if any must be submitted by the contractor to the engineer for approval prior to performing any additional repairs. Most engineers notify the contractor that they will not approve payment of repairs not expressly approved in writing.
The engineer’s specifications as well as International Concrete Repair Institute specifications and procedures provide specific criterions for proper concrete repairs. The most important is the requirement to excavate all concrete from around the reinforcing steel bars and two inches beyond the rusted metal, into “clean steel”.
After work begins, it is important to hold weekly progress meetings with the board representative, the engineer, the contractor and his supervisor to discuss the progress, any problems and suggested improvements to make the project run more smoothly. Minutes of the meetings (usually taken by the engineer) should be sent via e mail or fax in order to keep all parties up to date.
The Contractor – The next selection is a contractor with a minimum of five years experience in repairing similar buildings. The engineer is a good source for recommendations. So are board members or managers of nearby communities, as well as comments on contractors’ reputations by the local building department personnel.
While the engineer’s opinions are important, it is ultimately the board of directors who hire and must get along with, the contractor. The board of directors should review each of the contractor’s complete and detailed bids. Analysis of the bids should be predicated not only on price but also on the reputation, financial strength and a successful history of each bidder. At that time, usually three contractors are selected for in depth interviews with the board of directors and the engineer. This gives the board an opportunity to discuss the bid, the project schedule, and the manpower and equipment that will be used on the project. It is also very important to find out more about the contractors’ experience and the management team that will be involved with the project on-site or off-site, as well as any other concerns the board may have. The key to a successful project is communication between all parties and the interview will give the board members a sense of how comfortable they feel communicating with the contractor and its project team. Most boards of directors rely a great deal on their community manager (or hire a project manager) during the project. It is recommended that the manager and/or project manager be involved from the very beginning to gain a complete understanding of the project. This ensures that the board will be able to keep the unit owners informed on any changes to the schedule of the project.
Important Questions:
History of the company
Who are the owners of the company?
Who holds the State of Florida Certified General Contractor’s license?
The size of the work force
What equipment will be used?
Proper insurance coverage (General liability and workers’ compensation insurance)
The ability to secure payment and performance bonds (even if the association does not wish to have payment and performance bonds, the ability of the contractor to ascertain them is a good indication of their financial stability)
The Warranty
After the selection of the team, the next step is negotiation of the Contract. Some associations request that the attorneys handle this from the beginning, others request the contractor send a contract directly to the board to be reviewed. However, if the associations attorney will be ultimately reviewing the Contract it actually saves time to have them involved from the beginning. Otherwise the Contract is negotiated between the association and contractor and then the attorneys do it all over again.
Contract
A standard stipulated sum contract simply does not work for concrete restoration projects. While the scope of work is known, the actual “quantity” of the concrete requiring repair is just an estimate, based on the engineer’s inspection; the actual extent of the damage cannot be determined with any accuracy until the damaged concrete is chipped away. Because of this uncertainty, a “unit cost” contract has become the standard contract-billing format for concrete restoration work.
Under this type of contract, the owner pays only for repairs actually completed based on square footage, linear footage, or, in some repairs, cubic footage of concrete. The contract language will normally be negotiated between the association’s attorney and the contractor’s attorney and then
approved by the board of directors and the contractor. This ensures that the best interests of both parties are protected.
The Main Contract–Addresses the parties to the contract, the estimated contract sum, retainage, estimated time to complete the project, how to address change orders in the scope of work, insurance requirements, billing procedure, payment terms, and warranty. There may be other items that are unique to a specific project. The contractor must get any change orders with all relative information to the engineer and the owner in a timely manner, so that it can be reviewed and approved quickly for the least amount of negative impact to the project schedule.
General Conditions–Addresses standards of work, licenses, property damage and personal liability, insurance requirements, workforce standards, provisions of facilities and services, safety, work hours, and indemnification. There may be other items that are unique to a specific project.
Unit Price List–contains a list of repair items, unit measurement (SF, LF, CF, etc.) unit price, estimated quantities, and costs of mobilization and other items, such as permits and bonding. This is usually a direct copy of the contractor’s unit price proposal in response to the bid solicitation.
Engineer’s Project Manual–A project manual is written by the association’s engineer, usually a duplicate of the instructions to bidders and specifications that the contractors received prior to bidding the project.
An efficient contractor will prepare an additional packet of documents to be executed with the contract, including:
- · A Certificate of Insurance naming the association as additional insured.
- A Notice of Commencement Form. (must be signed by the “owner” and recorded at the courthouse)
- Permit Application prepared by contractor – Each building department in every municipality has completely different forms; there is no generic form.
- A letter to the building department on the association’s letterhead stating that it has hired the contractor to perform concrete repairs.
- A letter to the building department on the association’s letterhead stating that it has hired the engineer.
With these documents, the contractor can apply for the permit immediately.
Building Department
The local building department issues permits but, as previously mentioned, most building departments are not equipped to perform inspections for concrete repair projects; therefore, the association’s engineer will act as a “special inspector” to perform inspections and submit weekly inspection reports to the building department.
.
Pre-Construction Meeting
After the contractor is selected and the contract is executed, a pre-construction meeting is scheduled. The purpose of this meeting is to designate areas that will be available for the contractor’s trailer (field office) and other equipment, contractor employee parking, discuss a future meeting schedule, and address any other issues or concerns. A pre-construction meeting includes the board representative, the engineer and the contractor, as well as the supervisors that will be permanently assigned to the project. Seemingly, minor details like where to place dumpsters and port-o-lets or store job equipment and materials can become a source of annoyance to owners if not adequately addressed beforehand.
While the permit is being processed, the parties may choose to have the contractor mobilize the project meaning bring in scaffolding, equipment, dumpsters and port-o-lets so work can begin as soon as the permit is issued.
Survey of Building
Before beginning work on the building, the contractor should perform an existing condition survey of the building-usually done in video and written form. This documents the condition of the building and surrounding areas, such as landscaping, and eliminates any question as to the existing condition of areas later claimed to have been damaged during the progress of the work. This protects the association as well as the contractor.
The association’s engineer will mark where the contractor is to make repairs. Each engineer may be a little different, but the markings are done with a pencil or felt tip type marker that shows where and the size of the excavation required. For the repairs to be covered by the contractor’s warranty, the repairs must be made in accordance with the International Concrete Repair Institute (ICRI) standards, which specifies how and to what extent concrete repairs are made. The engineer performs additional inspections as the repaired areas are being prepped and new concrete is poured and cured.
Testing of repaired concrete is also performed by an outside, independent testing firm to ensure that the concrete has reached its required strength before additional work can be performed on those areas. There are times unit owners may wonder why it appears that work has stopped on a balcony and the contractor has started working on another area. This question usually occurs during the curing/testing period.
During the curing/testing period, the engineer will specify the strength of the concrete to be used per square inch (PSI); usually 5000 PSI. The concrete testing company will be on site when the concrete pour is being done and will take several cone shaped samples back to their lab. There the samples will be tested to see how strong they are at 7, 14 and 21 day intervals and send reports on each test. The forms for the concrete cannot be removed until the specified strength has been reached.
Billing Forms
Because the contract sum is not based on a stipulated sum, billing on a percentage of completion is not applicable to concrete restoration projects. Lump sum items such as mobilization, general conditions, and permit can be billed on a percentage, but are often billed in full, particularly mobilization and permit fees. For billing of completed concrete repairs, a detailed schedule of values will show the quantity of specific unit priced items completed during the billing period and to date.
The first page is a summary with the first part reflecting the original contract amount, any increases or decreases to the contract amount by change orders, increase/decrease of quantities, and adjusted contract amount.
The next section of the summary page shows the total amount of work completed to date, the amount of retainer being held, the total value of work performed less retainer, total of previous payments made to the contractor, and the amount of the payment due for the current payment requisition (draw).
There should be several pages included with each payment requisition that gives detail of where the work was done, including a drawing of the area. With new construction, everything is covered by the contractor’s warranty; however, in restoration projects only the repaired areas are covered under warranty. Many times an association will complain several years after completion of work that additional concrete is damaged. Unless that specific area was repaired in the previous project, the new damage will not be covered by warranty.
The best way to ensure the association’s warranty applies to the exact area repaired is to require the contractor to include with each payment application the summary page, the detail page, and spreadsheet for each unit showing measurements of each repair and a balcony drawing showing the location and nature of each repair made. This would be the equivalent of an “as built” drawing on new construction. This drawing also protects the contractor against unwarranted claims of defective work.
Warranties
Protecting the investment in the repairs is very important. Therefore, the concrete should be waterproofed and painted as soon as possible with materials and specifications designed for maximum protection. Many restoration contractors have the ability to provide waterproofing and painting as part of their bid.
The warranty on concrete restoration projects is normally five years on the concrete repairs and waterproofing. Alteration of the repairs, however, may void a warranty. If a unit owner installs tile or carpeting or penetrates the surface of the concrete to install items on a balcony, the warranty will likely be voided. Associations should provide copies of the warranty to all unit owners requiring them to sign as having received it. If the unit owner does anything to void the warranty without prior approval from the association, the unit owner will be responsible for damage not covered by warranty exclusions.
The concrete repairs performed in accordance with specified materials and procedures provide a very durable repair. Most warranties specify that if any problem is found in the area of the repair, the association’s representative must notify the engineer of record and the contractor in writing. Together they should examine the areas in question and refer to the “as built” drawings submitted by the contractor with each invoice. The engineer is the final judge as to whether the problem is covered under the warranty or if it is a new repair in an adjacent area.
The warranty issue is another important reason to hire a contractor with substantial resources and a history of honoring the warranties.
If other types of work are done in conjunction with concrete repairs, the warranties for that work can vary, depending on the type of work done and the products that are used. In addition, if the restoration project includes sliding glass doors, railings, and exterior painting, the association should also receive warranties directly from the manufacturer which are provided by the contractor with its final payment application.
Conclusion
The truth is restoration projects are a necessary evil. They cause noise, dust, and are not normally short projects. However, experience has shown that keeping the board, manager and unit owners informed creates a much better environment. The result is maintaining the value in the units as well as the safety of the residents.
Communication is key to the success of any project.