Nail Tips for Home Improvement Projects: A Do-it-Yourself Guide
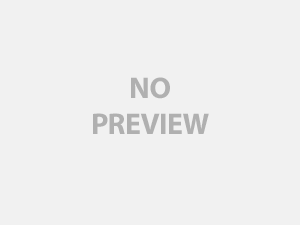
Probably the most common problem occurs when you fail to pre-drill properly for a screw. As you snug it down the last few turns, the torque on the shaft is just too much and the screw snaps off. Now you have to get the broken screw out. If you’re lucky, the screw will break off just below the head and there may be just enough shaft sticking up to grab with a pair of pliers. Get a good firm grip on the shaft – Vise Grip pliers work best – and carefully turn the screw back out. Pre-drill properly, drive a new screw and you are back on track.
More often, however, the screw will break off where the threaded section of the shank ends. In this case, the end of the shaft may be flush with the surface of the wood or even buried out of sight. In either case, you won’t be able to grab the shaft with pliers.If the screw is large enough – a number eight or higher – you should be able to get it out using a screw extractor. This is something like a specially hardened screw with very steeply pitched left-hand threads. Screw extractors are made in various sizes and are sold at hardware stores along with the chuck-like handle you need to grip them. Buy an extractor about half the diameter of your problem screw. When you buy the extractor, take a look at its shank. Stamped on the side should be the diameter of the drill you will need to bore a starter hole for the extractor. If you don’t have the proper size twist drill at home, buy one.
Back home, mark the center of the screw shaft with a center punch and drill the proper sized hole down into the center of the broken screw. Go about a half inch deep. Now put your extractor in its handle and start threading it into your pilot hole – turning counterclockwise – until the extractor binds. Then just keep turning. The extractor should get a good grip inside the broken screw, letting you back it out. Use this same technique with the screw extractor to remove screws with slots so chewed up a screwdriver will no longer work. Screw extractors are hard to use on small screws because it’s difficult to drill the necessary starting hole without sliding off center and chewing up the end of the screw. To solve this problem, use the technique shown in the sketch.
At the hardware store, buy a simple tool called a plug cutter. Normally, it’s used to cut wooden plugs used to cover the heads of counter-bored screws. But in this case, we won’t be interested in the plug. Chuck the plug cutter in an electric drill and use it to cut down about one-half inch into the wood. When you remove the cutter, you’ll see a neat, ring-shaped slot cut around the screw, which will be standing in the center of a small plug of wood.
Taking a small chisel, carefully chip away this plug. This will leave the shank of the screw exposed and you should be able to grip it with needle-nose pliers and twist it back out. If you have no needle-nose pliers, you should be able to tighten the chuck of your reversible drill around the screw shank. Put the drill in reverse, squeeze the trigger and the screw will come out.
If the screw is bound up so tight you can’t budge it, try heating the end of the screw with a soldering iron. This may char the wood around the screw just enough to loosen the bond between wood and screw. After you get the screw out, plug the hole with a length of dowel or some wood dough. You should be able to avoid all this fussing in the future if you drive screws properly in the first place. Always pre-drill the right-sized pilot hole before driving a screw. What’s the right size? About the same diameter as the shank of the threaded part of the screw. With big screws, lubricate the threads with some paste wax before you drive them. This will make the screws easier to drive and easier to remove when the time comes.
To avoid chewed-up slots, use Phillips screws whenever possible. Use the right-size screwdrivers with tips in good condition. Finally, don’t over-tighten any screws, and do not expect screws to pull loose joints together. It’s best to pull the joint up snug with a clamp first, then drive the screw.