How to Fix Cracked Copper Pipes
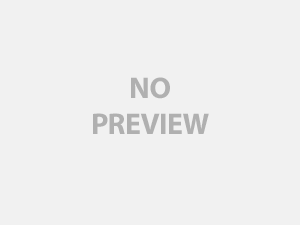
I was in for a surprise when I recently turned out the main outdoor valve. I found leaks all over the copper piping that runs throughout the backyard. I thought I would call a plumber, but quickly decided that paying someone to do this would cause me lots of embarrassment as Earl The Plumber would call me an idiot for not draining them last winter.
To fix a crack in a copper pipe, you must cut out the pipe where the crack is located, and place in a new piece of pipe. Simply wrapping the pipe with a tire tube and duct tape is not the recommended way of doing this. In order to fix the crack, you need a pipe cutter, flux, solder, copper couplers, and a blow torch.
The proper pipe cutter for copper is something that looks like the letter C with a screw in one end. Simply put the C around the pipe and turn the screw down as far as it can go. Then spin the tool around the pipe and watch as it digs into the pipe. Every few turns, crank the screw a little more to make the blade cut further into the pipe. After a few seconds of spinning the tool, the pipe will be cut. Cut a piece that extends a few inches before the crack to a few inches after the crack. Next, cut a new piece of pipe that is the same length as the one you just removed.
In order to put the new piece of pipe in place, a copper coupler is used. A coupler is a short piece of pipe that is slightly wider in diameter than the piece of pipe itself. There are two kinds of couplers. One is straight through all the way, and the other has a line inside of the coupler right in the middle. I prefer the coupler with the line in the middle, as it allows you to properly align both pieces of pipe right in the middle of the coupler for maximum support. Take the replacement pipe and coat each end of the pipe on the outside with flux. Enough flux should be placed on the end of the new pipe such that when the coupler is placed on the pipe the entire coupler is covered in flux. Next, put the flux all over the inside of both couplers. You will be placing a coupler on each end of the new pipe. Now, with flux on both ends of the new pipe, and flux on the inside of both couplers, put one coupler on each end of the new pipe.
At this point you should have a new piece of pipe with a coupler on each end of it. It is now time to solder the couplers to the new pipe. Fire up your blow torch and get your solder ready. Heat the coupler until you hear the flux start to pop. This is the sign that the pipe is getting hot enough. With the coupler hot, keep applying heat with the blow torch and place the solder on the top of the border between the coupler and the new pipe. When the solder gets hot enough, it will liquefy and by some crazy act of nature it will get sucked all around the pipe and complete the seal. I cannot explain how this takes place but it is fun to watch and it is simply amazing. Follow the previous steps to attach the coupler to the other end of the new pipe.
Now that the new pipe is ready to go, the next step is to prep the old pipe that is still in place. Two steps must be completed prior to attaching the new pipe. The first step is to make sure the existing pipe is clean at the connection points. My pipe was painted, so I used sand paper to clean the ends of the existing pipe down to the bare copper. Make sure this step is done as I almost burnt down my house when I fired up the blow torch and caught the paint on the pipe on fire. The second step is to make sure everything is dry on the old pipe. I just use paper towel and dry the existing pipe both on the inside and outside.
At this point we have a new piece of pipe with couplers on each end, and have prepared the two connection points on the existing pipe. We now need to put flux on the inside of the two couplers and on the outside of the two connection points on the existing pipe. With the flux smeared all over, place the new pipe in place. Do not worry about the pipe falling, the coupler is tight enough to hold it in place. Now simply solder in both connections as we did earlier.
After the pipe has cooled, cross your fingers and turn on the main valve. If everything has been done correctly, the leak should be fixed. Do not forget to cross your fingers, it is a really important step. Fixing cracked copper pipes is really easy, and can be done cheap and quickly.